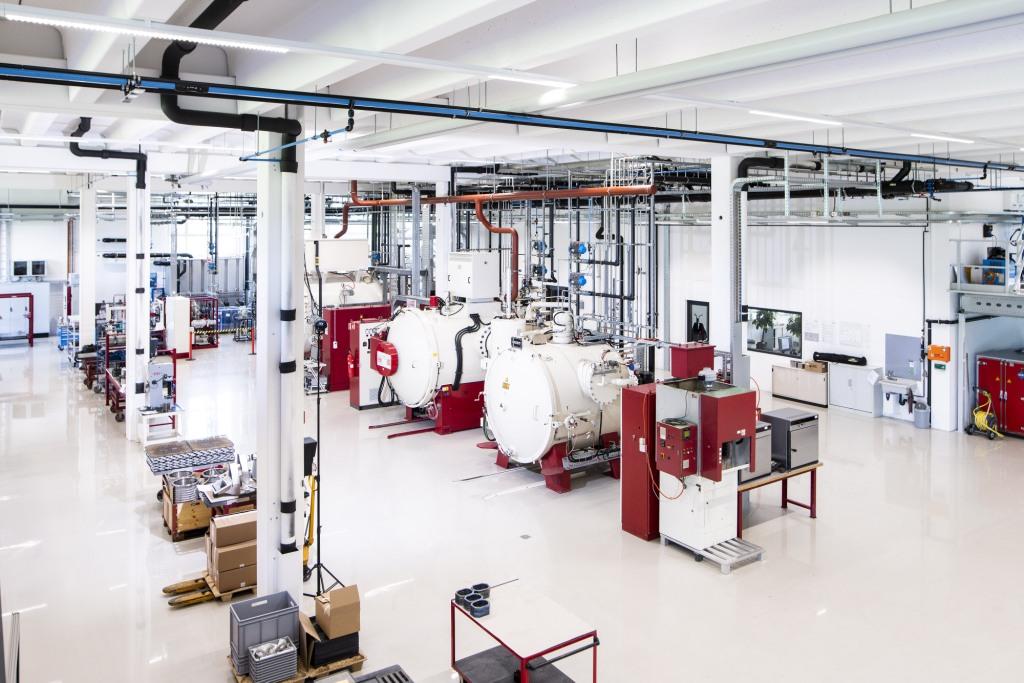
Starting from simple semi-finished products, complex components can be produced cost-effectively and/or the effort for pre- and post-processing procedures can be reduced. This increases significantly the flexibility with regard to function and costs.
The principle of vacuum brazing involves the joining of identical or different materials by using a brazing alloy as a filler material, which melts at high temperature in a vacuum atmosphere. The molten filler material wets the joining partners and subsequently bonds them to each other during cooling and solidification. The vacuum atmosphere inhibits a detrimental interaction of the brazing alloy and base materials with the environment and thus prevents damages to the components.
In contrast to other brazing processes, vacuum brazing does not necessitate any flux, which avoids defects in the bonding zone, leading to strength values in the range of the strength of the base material. This further avoids an oxidation of the components, even at high brazing temperatures. Thus, it is not necessary to remove flux residues, which are often corrosive, after the brazing process.
This universal joining technology enables developers and production managers to design and manufacture modular components. Starting from simple semifinished products, complex components can be produced cost-effectively, reducing the effort for preand post-processing procedures. The flexibility in the combination of components with fundamentally different masses, wall thicknesses, and geometries as well as the use of different material properties with regard to function and costs is significantly enhanced. Additionally, media-conducting components can be equipped with a complex, internal channel structure.
The vacuum technology allows to braze a wide range of materials, from single structural steels to high-alloy cold and hot work steels, to super alloys, as well as non-ferrous metals such as copper and titanium and even ceramics, hard metals, and the cutting materials cBN and diamonds.