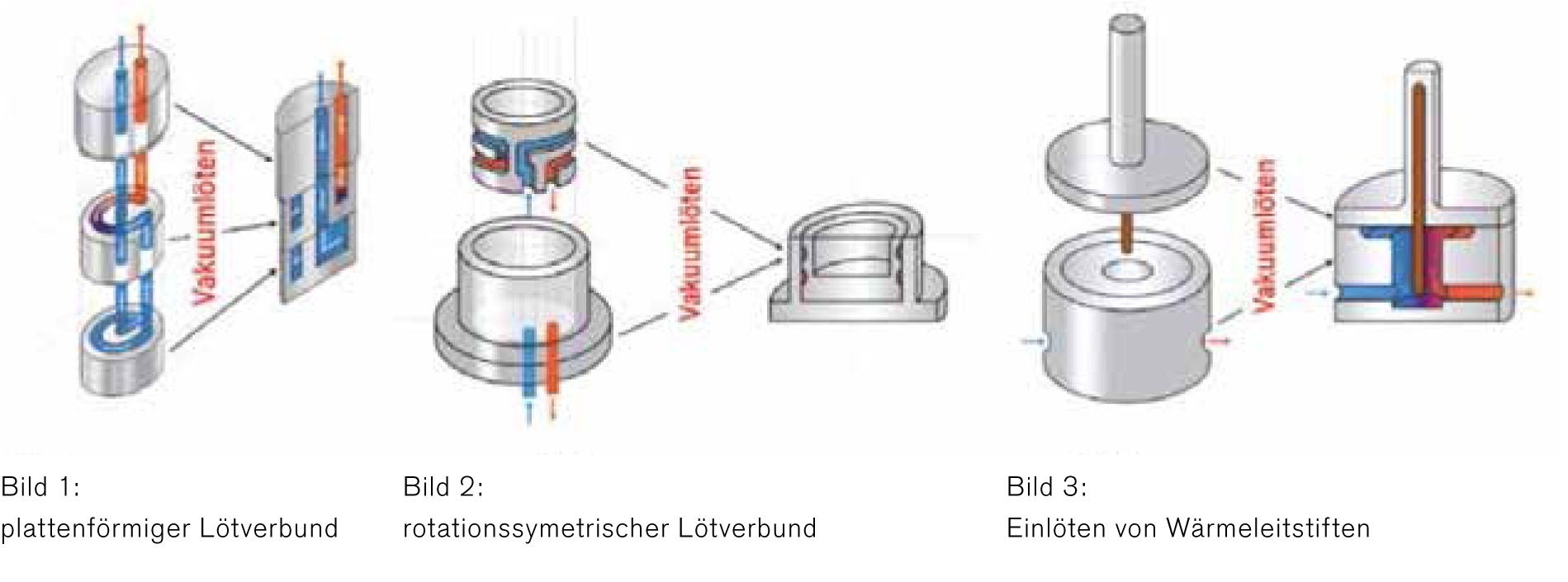
In order to achieve an optimum part quality with short cycle times an efficient mould temperature control is mandatory.
Vacuum brazing enables the production of simple and flexible tools, such as injection moulds and inserts with a conformal cooling design, which not only improves the quality of the components but further reduces the time of the production cycles. Hardening according to customer specifications with this technology is effectively free of charge.
This manufacturing technology additionally opens new possibilities in terms of design and material combinations within the field of mould making. Today, this approach is used in many areas of application, ranging from simple mass-produced components to complex components exposed to high stresses as for example in turbine industry.In order to achieve a conformal cooling design, the tool is divided into several components in accordance with the direction of the cooling channels. Subsequently, any complex design of the cooling channels can be placed into the component by means of simple mechanical processing (Figs. 1+2). This cannot be achieved by conventional drilling and plugging.
Subsequently, the individual components are firmly joined in a vacuum furnace into gas-tight and highstrength functional units. If the desired areas of the tool cannot be reached with channels, it is possible to braze materials with a good thermal conductivity to the tool steel using a metallurgical bond (Fig. 3). The brazing layer thickness is only approx. 50 μm. Thus, the good thermal conductivity, e.g. of copper, can almost always be completely used. In any case, the heat transfer is significantly better than with pressed-in copper pins.
Advantages in Heat Treatments:
The brazing temperature is selected so that it corresponds with the hardening temperature of the steel used. This allows the hardening of the tool to be performed within the same process. In addition to cold and hot work steels, PM steels or nitrogen alloyed steels can be brazed and hardened as well. After hardening, the component is tempered to the hardness specified by the customer. If tools are to be coated after final machining, deep-freezing can further increase the dimensional stability of certain steels.