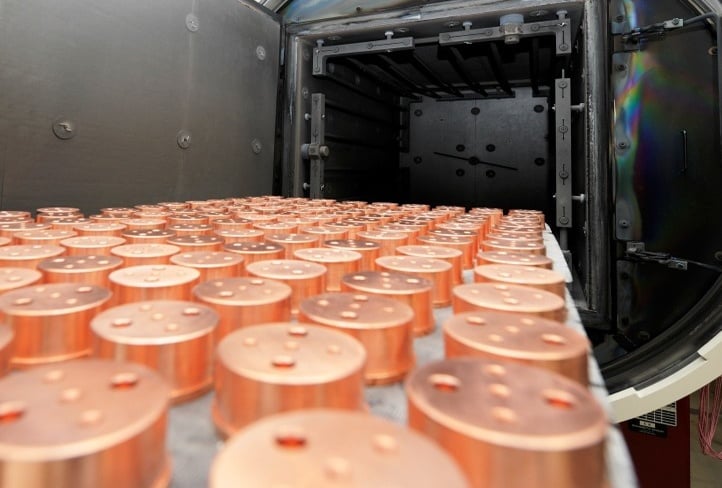
Hard- and high-temperature vacuum brazing is a joining technology which can be used to produce firmly bonded connections and to join complicated geometries or rather several joints simultaneously.
Vacuum brazing is characterized by its great universality and flexibility and has the following advantage:
-
An almost unlimited range of materials can be used (base materials and brazing alloys)
-
Minor distortions due to an even furnace heating
-
Very good joining quality due to the vacuum atmosphere
-
High strength, even at high operating temperatures
-
Avoidance of fluxes
-
High reproducibility due to excellent temperature uniformity and comfortable control of modern furnace systems, including the process documentation
-
Possibility of a combined heat treatment (brazing and hardening)
-
Large-scale components can be joined
-
No oxidation and annealing colour
-
Hardening and annealing can be integrated into the process
-
Low environmental impact
The disadvantages of vacuum brazing are:
-
Mostly batch processes with single batches. A continuous production is only possible with a very complex manufacturing facilities
-
Eventually high effort to fix components as components cannot be manipulated in the furnace
-
The whole component is heated, leading to a decrease of the hardness with already quenched and tempered materials or work-hardened materials
-
High investment costs